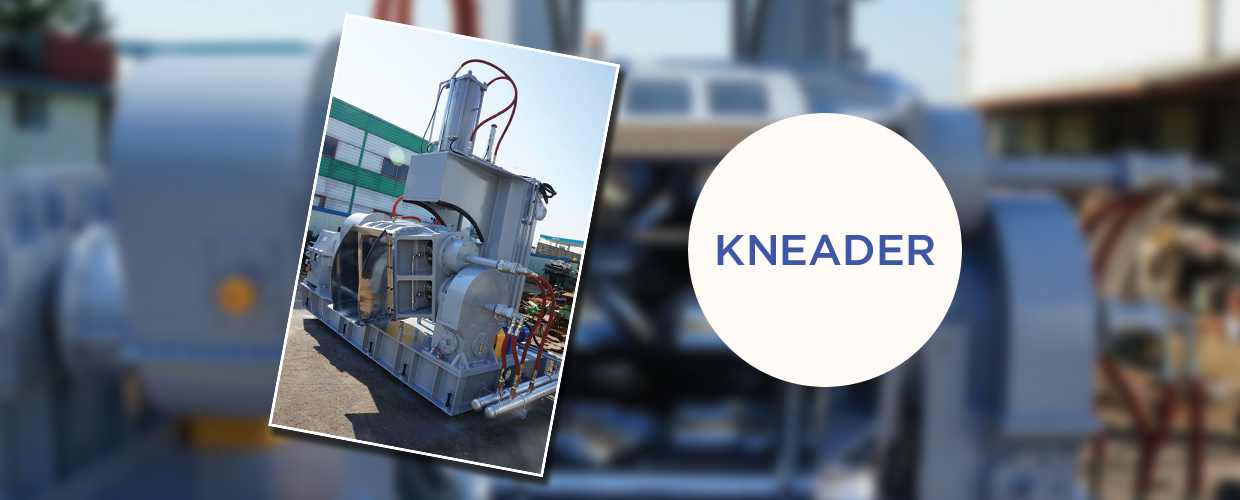
ViamTek dispersion Kneader are widely recommended for mastication master batch production. design with high precision, it is suitable for proper mixing and dispersion of carbon and numerous of raw material like natural rubber, synthetic rubber and more to improve the compound quality with help of correct blade angle to offering shearing action. High speed, excellent performance, Automatic temperature control, operating process are simple, and product quality are stable.
ViamTek offer Front Feeding- Front Discharge & Rear Feeding Front Discharge for flowing smooth production & rear charging window design also allows observation of compound mixing conditions. The compound dumping with mixing chamber has a 130° inclination for easy removal. The machine easy to install no needs of foundation, rate of failure are very less, simple maintenance.
Silent Features
- Capacities ranges from1.6L lab mixer to 100L production mixer.
- The Mixing Chamber is specially designed with heat resistance, wear out resistance.
- Specially designed rotor geometry is accurate machined to get better shear load and movement of material from one end axially. This ensures uniform mixing batch to batch and higher productivity.
- Pneumatic operated Pressure lid.
- Uni-drive Gear Box
- STD Make main motor.
MATERIAL CONSTRUCTION OF DISPERSION KNEADER
MIXING CHAMBER: Alloy Steel, Fabricated Hard faced, jacketed (both longitudinal & transverse) for steam heating & water cooling. The self-cleaning mixing chamber is duly polished and hard chrome plated, adding a best service life to the machine with an adjustable tilting angle (max. 140) for easy discharge.
MIXING ROTORS: Made of alloy cast-steel, spirally annular design, with node tips internally cored for effective Temperature Control. The Land of the nodes are hard & profile ground.
PRESSURE LID: Steel fabricated hard faced at mixing contact area, Jacketed for effective heating / cooling
DUST SEALS: Specially designed to keep environment Cleanliness & are easily replaceable.
DUST EXHAUSTING DEVICE: Hovering Vapours / dust, absorbed with suction blower or dust collector to common Exhaust duck.
SEQUENCE CONTROL: Either Manual push button electrical control or Automatic by electrical Control panel with P.L.C. timer based system as an optional feature as per client requirement
TEMPERATURE INDICATION CONTROL: Temp. Indicators with Thermo probes equipped with mixing chamber to give the exact mix temperature. Automatic Temperature control device with water pump & contact thermometer can be provide as an optional feature.
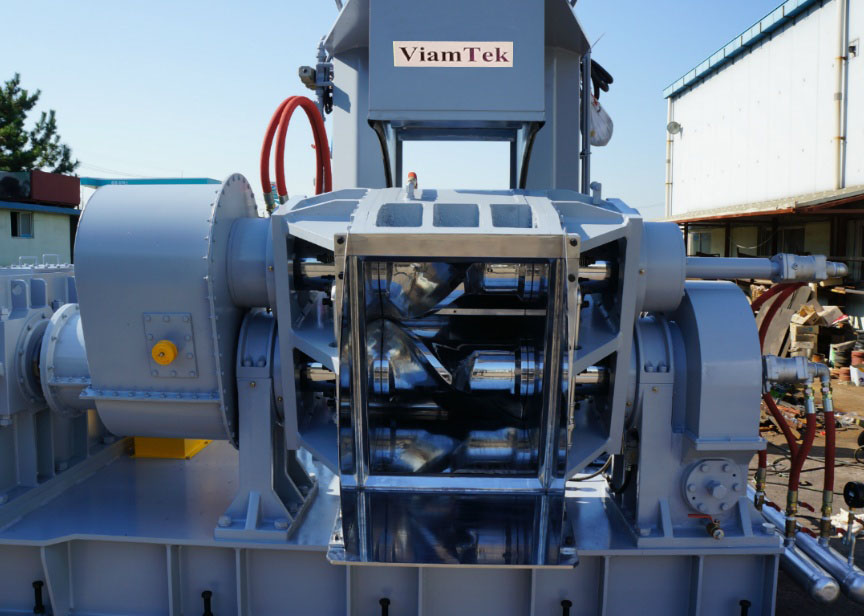